Tubular busbar conductor generally aerial installation after welding, using a dedicated tube bus hardware is fixed, because the strength of the joint is reduced after welding (about 65% of the parent metal), to avoid the overhead in using bent after joint, joint internal liner was used to reinforce, pillar (or suspension point) between two overhead welding head should not be more than two, commonly used aluminium and aluminium alloy pipe welding method is as follows:
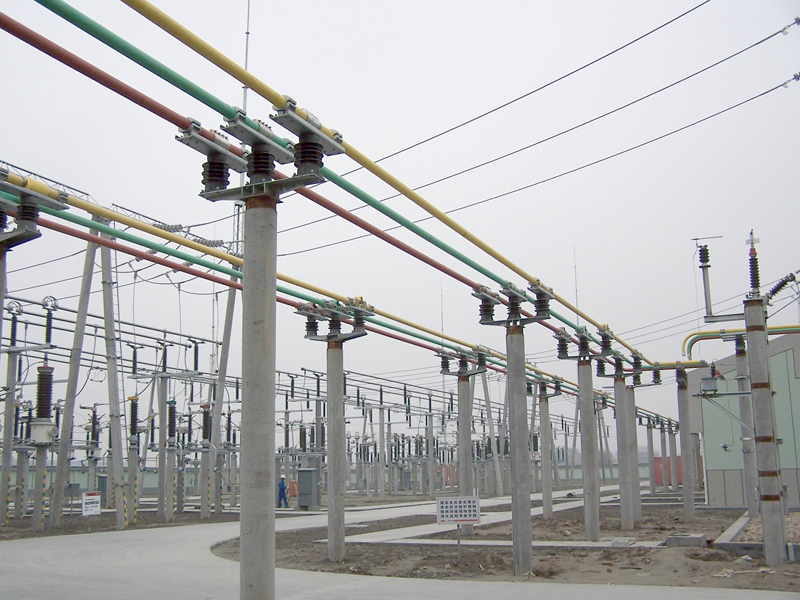
1. Argon requirements
The purity of argon should be above 99.9%, including impurity oxygen less than 0.005%, hydrogen less than 0.005%, water less than 0.02mg/L and nitrogen less than 0.015%.The increase of oxygen and nitrogen will worsen the atomization of cathode.More than 0.3% oxygen will aggravate the tungsten electrode burning loss, more than 0.1% oxygen will make the weld surface dull or black, more than 0.05% nitrogen fluidity of the weld pool becomes bad, the welding surface forming is bad.
Welding of aluminum-magnesium alloy tube bar 3A21 (LF21) aluminum-manganese alloy tube bar LDRE (6R05) aluminum-magnesium silicon alloy tube bar.
Tubular busbar conductor usually use aerial installation after welding (aluminum and aluminum alloy pipe welding way similar), after the overhead pipe type conductor adopts special bus hardware is fixed, because after welding the joint strength decreased (62% of the national standard requirements for wood), then use bent to avoid overhead after tapping, tapping the internal liner was used to reinforce, between two pillar overhead welding head should not be more than two, commonly used aluminium and aluminium alloy welding method is as follows:
Argon arc welding (MIG welding), argon arc welding is under the argon gas protection, using ac or dc welding power source, through the refractory tungsten as not consumable electrode, make it with workpiece produce arc, the melt filling materials and welding workpiece interface, compared with the welding, it has the advantage of centralized heat, arc stability, good protection of molten metal can get argon, avoid oxidation, and oxide film on the surface of the molten metal through argon arc be removed without welding flux, so both can get less defects and pure quality of weld, and can easily master the welding technology and can make all position welding.